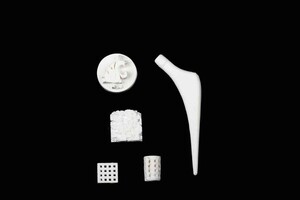
It sounds like something from a science fiction plot: so-called three-dimensional printers are being used to fashion prosthetic arms and hands, jaw bones, spinal-cord implants -- and one day perhaps even living human body parts.
While the parts printed for humans so far have been fashioned from plastic, metal and other inorganic materials, researchers in California and elsewhere also have begun printing living tissue, with the goal of eventually employing these "bioprinters" to create customized kidneys, livers and other organs for people needing transplants. What's particularly attractive about the technology, according to its proponents, is that 3D printers can produce body parts much quicker and cheaper than other methods.
Washington University biomedical engineering students designed and built a robotic prosthetic arm for teenager Sydney Kendall, 13, of St. Louis, Missouri. Sydney requested that her new arm be pink. She lost her arm in a boating accident when she was 6 years old. (Robert J. Boston -- Courtesy Washington University in St. Louis)
"You can make things for tens of dollars rather than thousands of dollars," said Stanford University professor Dr. Paul Wang, a cardiovascular and bioengineering expert who is among those studying the printers' potential for prosthetics, replacement bones and other applications. "It's totally opened up what's possible."
Developed in the 1980s by physicist Charles Hull, 3D printers have been used to make everything from jewelry, toys and guns to smartphone cases, car components and portions of NASA's robotic Mars rover. Last year, a Chinese firm even constructed a five-story apartment building from 3D-printed walls and other pieces.
Although the process varies, 3D printing typically involves using an inkjet-like printer that extrudes layer upon layer of substances into shapes digitally fashioned with computer-aided design software. Applied to medicine in recent years, the technology is producing remarkable results. People missing limbs or suffering other physical problems have been outfitted with printed arms, hands, shoulder joints, heel bones and portions of spines, hips, faces and skulls, among other things.
Bespoke Products of San Francisco 3D-prints "fairings," which fit around prosthetic legs to make them look more natural. And a researcher for San Rafael-based software company Autodesk is helping Ugandan officials learn how to print other prosthetic leg parts for children in that country.
But among the most ambitious dreams for the technology is that it will prove useful for making implantable human tissue, especially organs, which are in short supply, said Carlos Olguin, who is part of an Autodesk research team he describes as "looking at life as a new design frontier." Replacement organs, he said, are a "need that is not being satisfied at all in many cases."
One company working on that problem with Autodesk's help is Organovo of San Diego.
Six-year-old Alex Pring of Groveland, Fla., tries out the prosthetic arm created for him by a team of engineering students at the University of Central Florida. The arm was created for a cost of around $350 using off-the-shelf electrical servo motors and custom machined components created on a 3D printer. A similar conventional prosthetic arm would cost $40,000. (Katie Manero)
Using a combination of cells in what it terms "bio-ink," Organovo already has 3D-printed blood vessels as well as liver, lung and breast-tumor tissues for laboratory studies of potential treatments for cancer, Parkinson's disease and pulmonary hypertension. Although the company has yet to be profitable since it was incorporated in 2007, it has forged partnerships with several research institutions and drug companies, including giant Hoffman La Roche.
Many experts caution that printing viable replacement organs will prove extremely difficult, especially for such complex organs as the brain. In addition, it's hard to print the blood-vessel networks needed to replenish organs with oxygen and nutrients. Nonetheless, University of Pennsylvania researchers say they've designed a way to print those networks and a Russian company, 3D Bioprinting Solutions, has vowed this year to 3D-print a transplantable thyroid gland, which is laced with blood vessels.
Still other researchers are 3D-printing insulin-producing pancreatic tissues to help manage diabetes, viruses that can attack cancer cells and organ models that surgeons can practice on or that can be used to help design medical devices.
Stanford's Wang, for example, has made a 3D-printed model of the heart along with a prototype of a tiny gadget he envisions one day could crawl though real hearts to gather information on the organ's health or kill cells that damage it.
The business-information firm Visiongain has estimated that the 3D-printing medical market could generate about $4 billion in 2018. But Lux Research, which tracks emerging technologies, has a far more conservative forecast. Assessing the current market at $25 million annually, it projects the business will reach no more than $638 million by 2025.
One of the biggest challenges for the industry will be convincing the government of the safety and efficacy of implanting bioprinted tissues into people, said Anthony Vicari, a Lux research associate.
"I think it's going to be held back more than some of the advocates expect by the difficulty of getting regulatory approval," he said. "That's likely to slow things down."
Attracting potential investors could be another barrier, said Shaochen Chen, a UC San Diego nanoengineering professor experimenting with 3D printers to make blood vessels and a liver-like device that can remove blood toxins.
Although he believes the business "will be big," he added, "this is a relatively new field and it takes a while for people to recognize its importance."
Yet despite such challenges, many people are encouraged by the impact 3D printing already is having on health care.
"It's going to be a long road; there are a lot of hurdles ahead of us," said Michael Renard, Organovo's executive vice president for commercial operations. "But there is a lot that's showing us it's worth continuing to move forward."
Contact Steve Johnson at 408-920-5043. Follow him at Twitter.com/steveatmercnews
Ears
Team: Cornell University How it's made: Bioengineers take a 3-D scan of a child's ear, design a seven-part mold in the SolidWorks CAD program, and print the pieces. The mold is injected with a high-density gel made from 250 million bovine cartilage cells and collagen from rat tails (the latter serves as a scaffold). After 15 minutes, the ear is removed and incubated in cell culture for several days. In three months, the cartilage will have propagated enough to replace the collagen. Benefit: At least one child in 12,500 is born with microtia, a condition characterized by hearing loss due to an underdeveloped or malformed outer ear. Unlike synthetic implants, ears grown from human cells are more likely to be successfully incorporated into the body.
Kidneys
Team: Wake Forest Institute For Regenerative Medicine How It's Made: A 3-D bioprinter deposits multiple types of kidney cells—cultivated from cells taken by a biopsy—while simultaneously building a scaffold out of biodegradable material. The finished product is then incubated. The scaffold, once transplanted into a patient, would slowly biodegrade as the functional tissue grows.Benefit: An estimated 80 percent of patients on organ-transplant lists in the U.S. await kidneys. Bioprinted kidneys are not yet functional, but once they are, the use of a patient's own cells to grow the tissue means doctors will someday be able to provide every recipient with a perfect match.
Blood Vessels
Team: University of Pennsylvania and MIT How it's made: Using an open-source RepRap printer and custom software, researchers print a network of sugar filaments inside a mold and coat the filaments in a polymer derived from corn. They then dispense a gel containing tissue cells into the mold. Once it sets, they wash the structure in water, which dissolves the sugar and leaves empty channels in the tissue. Benefit: Researchers showed that pumping nutrients through the channels increased the survival of surrounding cells. Because blood vessels maintain tissue health, learning how to scale up and print a larger, more robust vascular system is the key to eventually printing entire organs.
Skin Grafts
Team: Wake Forest Institute for Regenerative Medicine How it's made: First, a custom bioprinter scans and maps the patient's wound. One inkjet valve ejects the enzyme thrombin, and another ejects cells mixed with collagen and fibrinogen (thrombin and fibrinogen react to create the blood coagulant fibrin). Then, the printer deposits a layer of human fibroblasts, followed by a layer of skin cells called keratinocytes. Benefit: For traditional grafts, surgeons take skin from one area of the body and splice it onto another. The Wake Forest researchers hope to print new skin directly into a wound. Ultimately, they plan to build a portable printer that can be used in war and disaster zones.
Bones
Team: Washington State University How it's made: Researchers print scaffolds with a ceramic powder (human bone is 70 percent ceramic), using the same 3-D printers that produce metal parts found in electric motors. An inkjet covers the ceramic with a layer of plastic binder. This structure is baked at 2,282˚F for 120 minutes and placed into a culture with human bone cells. After a day, the scaffold supports them. Benefit: Every year, millions of automobile-accident survivors suffer from complex fractures, which are difficult to repair using traditional methods. Using MRIs for reference, doctors could print a custom graft that perfectly matches the fracture.
By Steve Johnson / sjohnson@mercurynews.com
http://www.mercurynews.com/business/ci_27412983/3d-printers-make-human-body-parts-its-happening
and
http://www.popsci.com/science/gallery/2013-07/5-body-parts-scientists-can-3-d-print
Kommentare
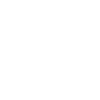