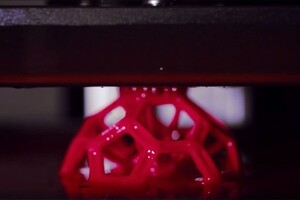
3D printing startup Carbon3D has demonstrated a new approach to fabricating commercial-quality objects from resin using oxygen and light.
On stage at the TED conference in Vancouver, CEO Joseph DeSimone ran through how it works, while one of the company's machines produced a plastic ball in about ten minutes. "It would traditionally take up to ten hours to print this," said DeSimone.
The process, which is called CLIP or "continuous liquid interface production", applies both oxygen and light to a pool of resin. The light hardens it, while the oxygen prevents hardening.
By controlling both factors carefully, complex shapes can be drawn out of the resin extremely fast -- between 25 and 100 times more rapidly than traditional approaches, with a feature resolution of one millimetre. DeSimone says he reckons he can get it up to 1,000 times faster. It was apparently inspired by the scene in Terminator 2 where the T-1000 rises up from a pool of liquid metal. Here it is in action:
Carbon3D DemoCarbon3D Brand
Right now it only works with polymer-based materials, but DeSimone says that the firm is "working on" others. Its machines are currently being tested by an automotive firm, an athletic clothing company and a research lab, and a commercial product should be out "within a year".
Possible applications, according to DeSimone, include custom-made medical implants -- such as teeth that could be printed "while the patient sits in the dentist's chair". The company has raised $40 million (£27 million) to commercialise the process.
"Current 3D printing technology has failed to deliver on its promise to revolutionise manufacturing," said DeSimone. "Our CLIP technology offers the game-changing speed, consistent mechanical properties and choice of materials required for complex commercial quality parts."
The team has detailed its process in a paper in the journal Science.
http://www.wired.co.uk/news/archive/2015-03/18/carbon3d-ted
Kommentare
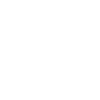